传统生产过程最底层为OT(Operational Technology),该层主要布置现场总线。中层为MES层,最上层为IT(Information Technology)层。随着网络的普及应用及数字工厂的提出,现代生产过程的组织、生产流程的规划等步骤已逐步下沉到OT层。
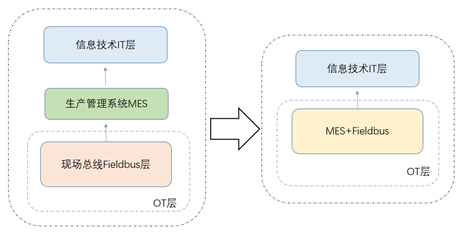
图2 工业生产传统3层结构向现代2层结构的转变
基于此,本实验将MES系统融入现场总线所在的OT层,学生在设置协同生产过程的同时,可以在OT层系统地了解掌握完整生产信息,甚至其它厂家的生产信息。
(1)通过本实验,学生掌握分布式工厂不同地域节点配置方法;
(2)针对具体生产过程,学生掌握工艺流程设计的方法;
(3)能正确分析一道工序,综合所需信息来分析、解释实验结果,并得到合理有效的结论
MES与现场总线集合的底层生产技术
轮胎生产由本地生产及异地生产联合构成。本地生产结构如图1所示,主要技术为现场总线技术。现场总线是连接智能现场设备和自动化系统的数字式、双向传输、多分支结构的通信网络。在本实验中总线应用在生产现场,在轮毂、螺帽、盖板的底层智能测控设备之间实现双向串行多节点数字通信的系统。具体来说,底层冲压、CNC(计算机数控)、热处理等工序的传感器与执行器信息由总线网络传输至主控制柜,主控制柜与服务器之间由现场总线网络传输,服务器与上层工程师站由以太网连接,并由TCP/IP局域网连接工厂管理者。现场总线网络依靠总线型拓扑可以连接多个现场节点,从地域范围、挂接设备规模等方面极大方便现场生产的管理与实施。
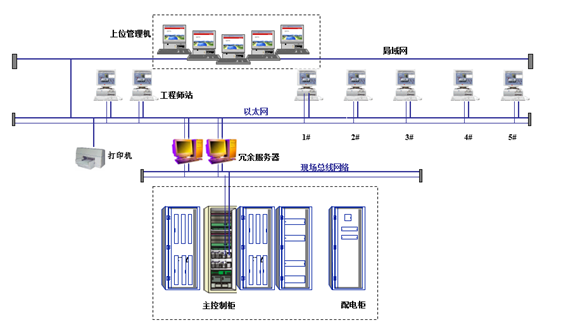
图1 本地生产网络拓扑
在传统的现场总线技术中,融合MES系统(生产管理系统),以网络联合构成底层生产。客户可以通过MES异地下单,生产管理者给不同地点的分工厂分配任务并排产,根据生产工序协同分工厂生产,最终产出产品。
本实验设置为综合实验,包含方案设计、工艺设计、生产管理等多个环节,实验内容丰富。本虚拟仿真实验的实验教学指导书全部嵌入系统,如图3所示。
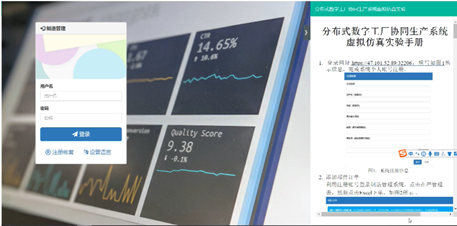
图3 系统界面
1)注册之后添加部件订单
利用注册账号登录制造管理系统。点击在产管理表,然后点击Excel下单。依次输入客户、工单号、名称、订单数量、备注、预定日期等即可录入部件订单信息。本实验以上汽客户为例,订单名称分别为轮毂、螺帽、盖板,录入相关信息后可点击提交,如图4所示。
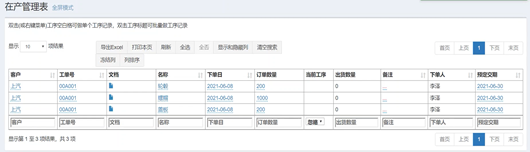
图4. 部件订单录入完成后界面
2)自定义工艺
点击自定义工艺及添加工艺, 完成轮毂、螺帽、盖板工艺添加,如图5所示。
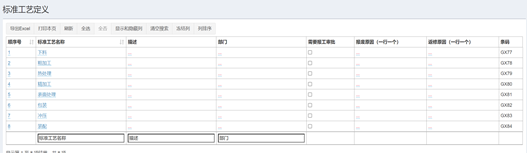
图5. 工艺添加后界面
3)SOP
点击SOP模块及工艺路线设置,针对轮毂、螺帽、盖板分别点击编辑SOP,完成SOP工序设计。轮毂SOP工序设计为下料—热加工—热处理—精加工—表面处理—装配—包装;螺帽工序为下料—冲压—精加工;盖板工序为冲压;其具体工时、工价、一出几等信息如图6所示。图7为Sop设置完成后界面。
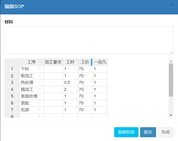
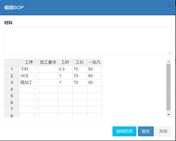
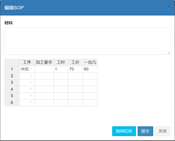
图6. 轮毂、螺帽、盖板SOP编辑界面
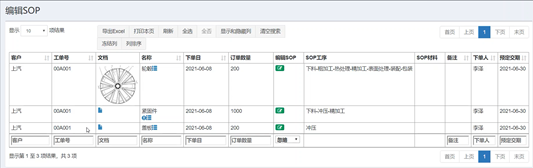
图7. Sop设置完成后界面
4)定义设备
在基础资料设备菜单下,点击添加设备,针对SOP工序设计所需的具体设备相关信息完成自定义设备。
5)定义员工
生产的工艺、工序、设备排好后,在基础资料员工菜单下,还可以编辑产线的员工及管理者,便于后续的移动端及管理端跟踪生产。
6)配置分布式账户
通过定义不同地点的分厂信息,分厂也可以实现与总厂一样的生产过程管理,最终实现协同生产。
7)分布式工厂生产流程跟踪-移动端
学生可以扮演产线员工,产线二维码,进入移动端进行生产跟踪。
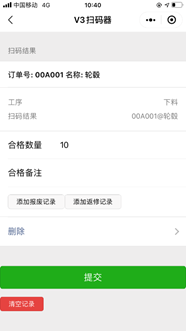
图8. 移动端跟踪生产
8)分布式工厂生产流程跟踪-管理端
学生可以扮演管理者从管理端进行报工(报产品完成情况)
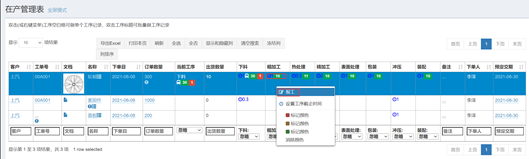
图9. 管理端跟踪生产
9)出货
最终完成生产订单的出货。

图10. 生产完成出货
10)生成报表
实验还可以通过生成过程信息及管理信息,如生产过程报表等数据图表,让学生了解生产的全部数据。
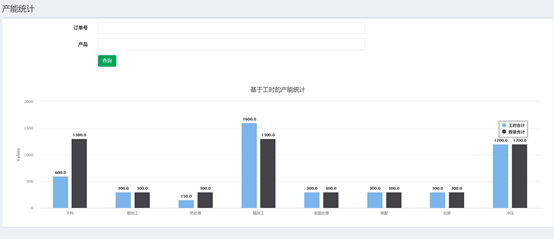
图11. 生成生产过程报表